HOT DIP GALVANIZING
Hot dip galvanizing (HDG) is also a common surface coating for steel fasteners. It provides a very solid and durable corrosion protection. Hot dip galvanizing for steel parts is standardized in ISO 1461, but for fasteners, the dedicated standard ISO 10684 exists. The process of hot dip galvanizing is quite simple: the fasteners are dipped in a bath of molten zinc with normal temperatures around 455°C to 480°C and high temperatures between 530°C and 560°C). Next, the fasteners are spun to remove the excess zinc, and then they are cooled in water to solidify the zinc. What remains is a layer of zinc (40 to 70 microns) on the surface of the products that is relatively thick compared to zinc electroplating (3 to 20 microns). Nuts are processed in the same way, except the nut thread is not yet formed. Nut threads must always be tapped after HDG. This tapping leaves the internal threads exposed (not covered with zinc), but it has no detrimental effects on the corrosion resistance, as illustrated further below. The HDG process is commonly regarded as suitable for fasteners with diameters M8 or larger.
The large amount of zinc provides excellent corrosion resistance in normal outdoor environments, but with the downside that its layer thickness is significantly above the thread clearance allowance, which this poses a problem for all threaded fasteners.
In order to cope with this issue, ISO 10684 provides two solutions, both of which involve changes in the dimensions of the basic threaded fasteners.
One solution is a system in which the externally threaded fasteners (bolts) are manufactured with a larger fundamental deviation such that the thread is made slightly thinner. After galvanizing, the bolt mates with an internal thread in thread tolerance class 6H (the ‘normal’ tolerance). The allowances of the external threads for this system are standardized in ISO 965-4 as thread tolerance class 6AZ (before galvanizing), and the system is designated as the ISO fit HDG system. Bolts are marked with property class and an additional “U.”
The other solution provided by ISO 10684 is to tap the internal threads (nuts) to be a bit larger (oversize) so that they mate with the galvanized externally threaded fastener (bolt), which is called the oversize HDG system. The nut oversize limits are standardized in ISO 965-5, and the thread tolerance class of the oversize tapped nuts is designated as 6AZ. Nuts are marked with property class and an additional “Z.”
The two systems must never be mixed, as mixing leads either to fitting problems (oversized bolt with ISO fit nut) or critical strength reductions of the threaded connection (ISO fit bolt with oversized nut).
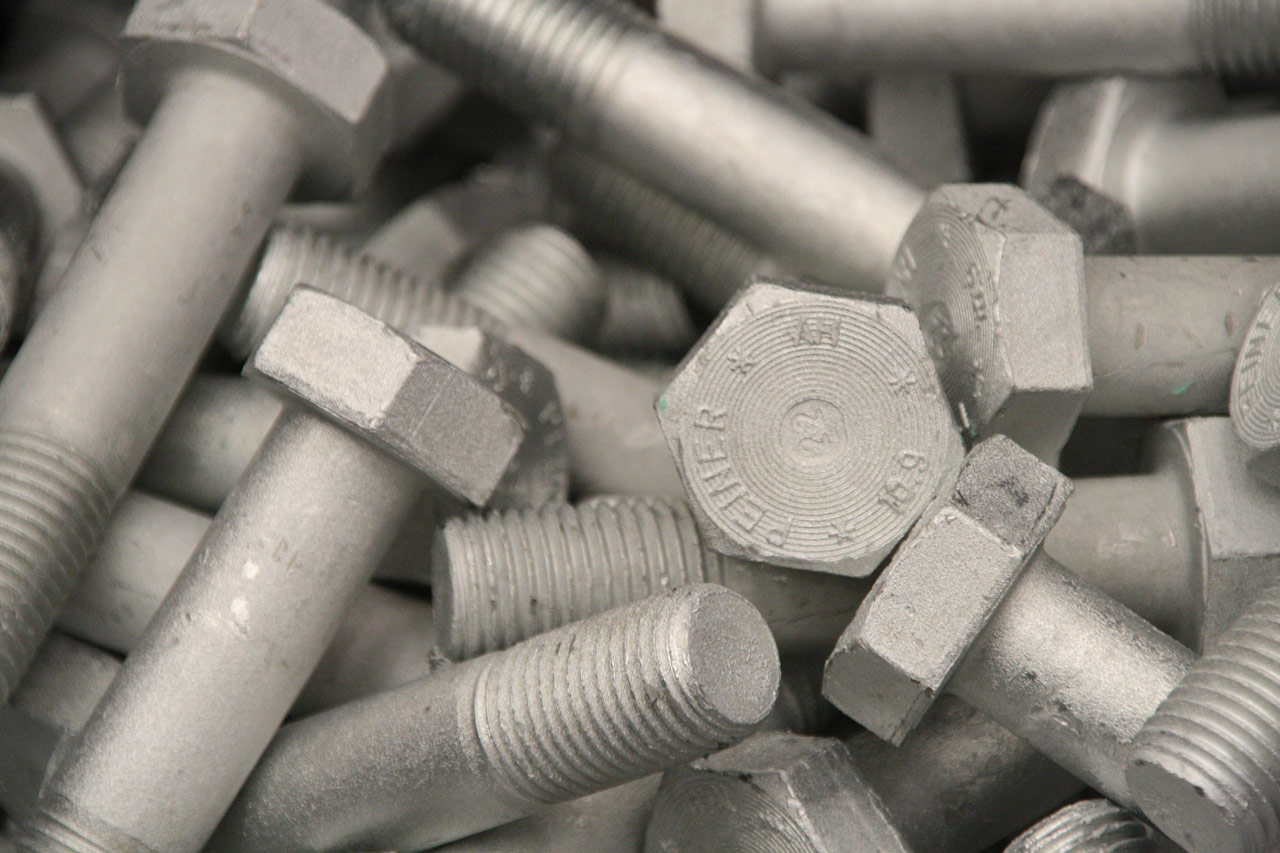
Source: Thielco Metal Coating
THREADED FASTENER LOAD ABILITY
Generally, it can be stated that the mechanical properties of the bolts in accordance with ISO 898-1 and the nuts in accordance with ISO 898-2 are not influenced by hot dip galvanizing. ISO 10684 only makes an exception for diameters M8 and M10 (in Annex A); for these dimensions, loadability is reduced by approximately 20%. Please refer to EN 10684 for details.
However, for the still very commonly used DIN 934 nuts, HDG is performed to DIN 267-10 (obsolete), and this standard allows for a reduction in loadability of all HDG fasteners. The loadability of a nut/bolt combination with DIN 934 nuts is reduced by approximately 5% for the largest size, M36, and this value gradually increases up to 20% for the smallest size, M6. Further specific values can be found in DIN 267-10. Due to the deviation of the thread tolerances, the screw thread of the bolt is allowed to strip at the minimum ultimate tensile load.
ATMOSPHERIC CORROSION ON HOT DIP GALVANIZED STEEL
When the coating is exposed to the atmosphere, a layer of corrosion products (zinc patina) is built up. This layer primarily consists of zinc carbonate, which, because it is almost insoluble, delays further corrosion. When galvanized, steel remains wet for a longer period, and there is insufficient air circulation. A white, voluminous zinc corrosion product, "white rust," may develop, though this product may be less desirable for reasons of aesthetics or painting. The formation of white rust can be suppressed by appropriate storage and packaging or, if necessary, by oiling the zinc or passivating it in chromic acid.
CLIMATIC INFLUENCE ON HOT DIPPED GALVANIZED STEEL PROTECTION
The time that steel remains protected from corrosion is proportional to the thickness of the zinc layer, and it is dependent on the climatic conditions, as shown in the graphic below. Generally, the amount of time that a zinc layer offers protection is interpreted as the time from the moment of exposure to the moment that base metal corrosion, “red rust,” can be seen on more than 5% of the surface.
Corrosion resistance under climatic influences:
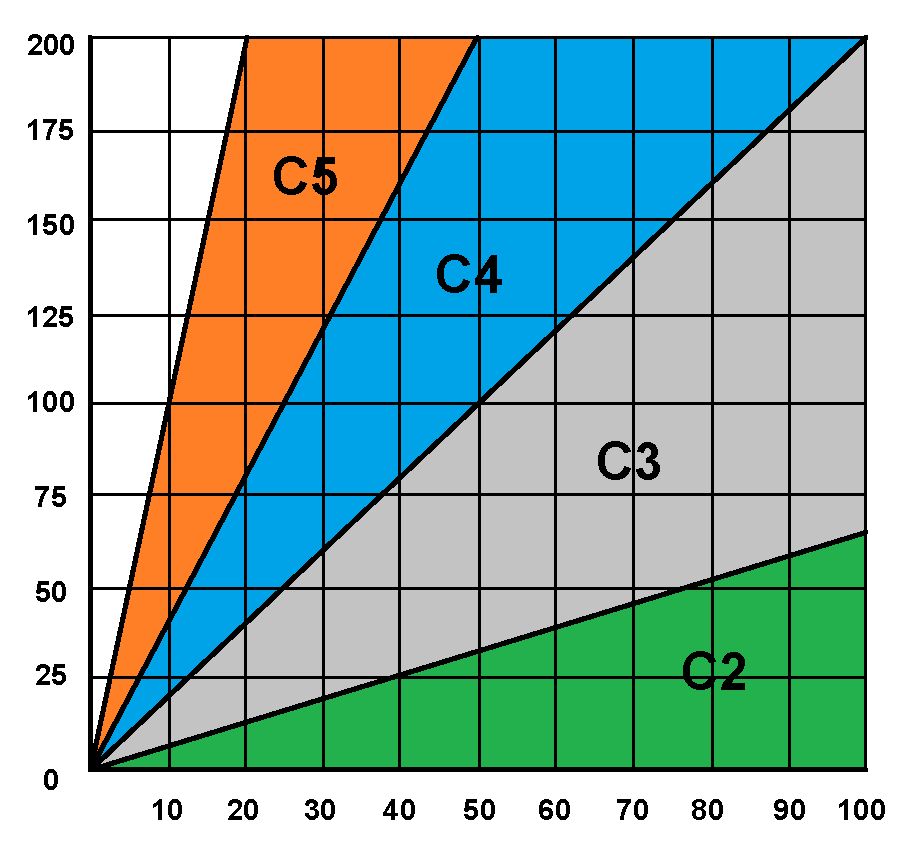
C2 - Continental climate
C3 - Larger city environments
C4 - Moderate industrial or coastal climate
C5 - Aggressive industrial climate
This graphic should be consulted only for rough estimates due to unforeseeable local influences.
SELF-HEALING EFFECTS OF HOT DIP GALVANIZED FASTENERS
In case the zinc coating is scratched or chipped, the zinc layer attempts to cover the damaged area in normal atmospheric environments.
Because zinc is less noble than iron (steel), the zinc dissolves first, which protects the steel against corrosion until all of the zinc has dissolved.
At locations where there are gaps in the zinc layer of 1.5 to 2 mm or on bare surfaces of up to 10 mm2, the steel remains protected by an electrochemical process, called “cathodic bridging.” The zinc provides sacrificial protection, and the unprotected areas are covered by a buildup of zinc salts. An example of this phenomenon is the screw thread of hot dip galvanized nuts that are tapped after galvanizing. The zinc layer on the bolt thread completely overtakes the protection of the uncoated nut thread. Another important aspect of cathodic protection is that no corrosion occurs underneath the zinc layer.
Schematic drawing of “Cathodic bridging”:

PAINTING HOT DIP GALVANIZED SURFACES
A so called duplex system is a combination of hot dip galvanizing and painting. It is a suitable solution in very aggressive atmospheres (e.g., near the sea or in an acidic environment), when maintenance and repairs are impossible to conduct, or when a special color is wanted. This system can offer 1.5 to 2.5 times longer protection than the sum of both separate systems. When properly degreased, hot dip galvanizing offers effective adhesion for many types of paint.