ELEKTROLYTISCH AANBRENGEN VAN ZINK OF VAN EEN ZINKLEGERING
Deze methode is met afstand de meest gebruikte oppervlaktebedekking voor bevestigingsmaterialen. Een zeer dunne laag (3 tot 20 microns* voor artikelen met schroefdraad) zink of een legering van zink (bijv. ZnFe, ZnNi) wordt op het product aangebracht met behulp van een elektrolytisch (galvanisch) proces. Zodra de artikelen zijn bedekt met zink, wordt een passivatielaag toegevoegd aan de zink- of zinklegeringlaag. Die dient als beschermlaag. Er bestaan veel types passivatie, met verschillende gradaties in corrosieweerstand en in verschillende kleuren.
*Een micron of μm is 0,001 millimeter.
Het elektrolytisch verzinkproces

Zoals het plaatje laat zien, worden de bevestigingsmaterialen in een roterende kunststof trommel gelegd en ondergedompeld in een tank gevuld met een elektrolyt (een geleidende vloeistof) en negatief geladen (kathode). Staven of platen van zink of van een zinklegering zijn eveneens in de tank aanwezig en worden positief geladen (anode). Zo transporteert de elektrische stroom de zink- of zinklegering-ionen naar de negatief geladen stalen bevestigingsmaterialen.
Zink of zinklegeringen zijn minder edele metalen dan staal. Indien gebruikt als beschermende laag functioneren ze als anoden. Deze anoden staan elektronen af aan het onderliggende staal wanneer corrosie dreigt in een vochtige omgeving. Dit heet kathodische bescherming.
Koper, messing, nikkel, chroom, tin en zilver zijn edelere metalen dan staal. Als deze metalen worden gebruikt als beschermlaag, gedragen zij zich als een kathode. Dit tast het staal rechtstreeks aan. Er kan zelf corrosie onder de beschermlaag ontstaan als vocht met het staal (anode) in aanraking komt door poriën in – of beschadigingen aan – de coating.
Dit is de reden waarom coatings met zink of zinklegeringen de meest wijdverspreide manier van corrosieprotectie zijn.
Passivatie (chromateren)
De bescherming die zink en zinklegeringen bieden, verbetert dankzij het passiveren van de producten. In de klassieke vorm van dit vervolgproces wordt een ultradunne (ca. 0,1 µm) chromaatlaag gevormd die de poriën in de zink- of zinklegeringlaag verzegelt en tevens zuurstof bindt. Deze chromaatlaag bevat vaak zeswaardig chroom (Cr(VI)) en bezit hierdoor een unieke ‘zelfherstellende’ werking. Bij mechanische beschadigingen herstellen de oplosbare zeswaardige chroomzouten in de passivatielaag de blootgestelde gebieden (herpassiveren). Het nadeel van deze nabehandeling is dat Cr(VI) wordt beschouwd als een schadelijke, milieuonvriendelijke substantie (giftig en kankerverwekkend). Het gebruik ervan binnen de EU is beperkt en Cr(VI) wordt geleidelijk aan verbannen door diverse Europese wetten (bijv. RoHS, ELV – zie de links aan het einde van dit document). Details over chromateren kunnen worden gevonden in de internationale norm ISO 4520.
Afhankelijk van de dikte en samenstelling van de passivatielaag varieert de kleur van transparant (wit) via blauwachtig en geel tot zwart.
Witte/blauwe passivatie
Dit is het meest voorkomende type passivatie voor bevestigingsmaterialen. Deze passivatie biedt een relatief geringe corrosieweerstand en wordt aanbevolen voor binnentoepassingen.
Zwarte passivatie
Deze passivatie biedt hetzelfde niveau van bescherming als witte/blauwe passivatie en wordt meestal gekozen vanwege het zwarte uiterlijk. Bevat Cr(VI).
Gele passivatie
Dit type biedt een betere corrosiebescherming en wordt geadviseerd voor buitentoepassingen, hoewel de populariteit ervan afneemt omdat het gehalte aan Cr(VI) groot is.
(Olijf-) groene passivatie
Deze types zijn voornamelijk bestemd voor militaire toepassingen. De corrosieweerstand ervan is gelijk aan of iets beter dan gele passivatie. De types bevatten eveneens Cr(VI).
Passivatie met driewaardig chroom (Cr(III))
Als gevolg van diverse wetgevingen op het gebied van schadelijke stoffen zoals RoHS, REACH en ELV moest een nieuw type passivatie worden ontwikkeld. Deze nieuwe passivatie zou geen Cr(VI) meer mogen bevatten. In plaats van Cr(VI), aanwezig in de zwarte, gele, groene en bruine chromaatlagen, maken de meeste nieuwe passivatielagen gebruik van driewaardig chroom (Cr(III)). Sommige van deze types bezitten zelfs betere corrosiewerende eigenschappen dan Cr(VI) houdende lagen. Deze worden vaak aangeduid met de termen ‘thick layer passivation of Dickschichtpassivierung’ (dikke-laag passivatie). Een ‘dunne’ laag meet tussen 0,08 en 0,1 µm en een dikke laag in dit verband meet 0,2 tot 0,3 µm. De passivatie met een dunne laag wordt het meest toegepast. Dikke-laag passivaties hebben een iriserend uiterlijk (blauw-geel-groenachtig op zinklagen, geel-groenachtig op zinklegeringlagen) en bieden een superieure corrosiebescherming, beter dan de Cr(VI) gele chromatering. In het verder verhogen van de corrosiebescherming en/of het verbeteren van de passivatielaag, kan nog een verzegeling (sealant) worden toegepast.
Waterstofbrosheid
Het elektrolytisch proces maakt gebruik van elektriciteit om de zink of de zinklegering neer te laten slaan. Maar, de elektrische stroom veroorzaakt ook een (gedeeltelijke) ontleding van het water in het bad in zuurstof en waterstof.
De zuurstof verdwijnt uit de vloeistof in het bad, maar de waterstofionen kunnen diffunderen (binnendringen) in het metaal van de bevestigingsmaterialen en zich binden tot waterstofmoleculen. Dit gaat gepaard met een toename in volume, waardoor grote spanningen in de metaalstructuur optreden. Bij grote externe trekkrachten kan een uitgestelde, spontane brosse breuk ontstaan. Overigens kan het beitsen zonder inhibitoren (beitsen zoals toegepast in het thermisch verzinkproces) en het ondeskundig veredelen van staal met hoge mechanische sterkte tijdens fabricage, ook waterstofbrosheid veroorzaken.


Het risico op waterstofbrosheid bestaat bij de volgende producten:
- met een treksterkte ≥ 1000 MPa
- met een hardheid ≥ HV320
- oppervlaktegeharde producten
In het beperken van het risico op waterstofbrosheid tot een minimum, moeten de behandelde producten na het elektrolytische proces voor een bepaalde tijd en op een bepaalde temperatuur opnieuw worden verhit (baked). De huidige internationale norm voor elektrolytisch aangebrachte beschermlagen op bevestigingsartikelen - ISO 4042 editie 1999 - stelt dat elektrolytisch gecoate onderdelen binnen 4 uur en liefst binnen een uur na het elektrolytisch proces en vóór het passiveren verhit (gebakken) moeten worden. Dit moet op een temperatuur van 200°C à 230°C. De maximum temperatuur moet worden bepaald met inachtneming van het materiaal van de coating en het type van het basismateriaal.
Met toenemende laagdikte wordt het verwijderen van waterstof moeilijker. Als dikke lagen moeten worden aangebracht kan een tussentijdse verhitting, (bij een laagdikte tussen 2 µm en 5 µm), het risico op waterstofbrosheid verminderen.
ISO 4042 geeft geen exacte aanwijzingen voor het verhitten. Een typische tijdsduur voor het verhittingsproces wordt gegeven als 8 uur. Echter, verhittingstijden van 2 tot 24 uur bij 200°C à 230°C kunnen van toepassing zijn. Dit hangt af van het type en de afmeting van het product, de geometrie, de mechanische eigenschappen, de reinigingsprocessen en het toegepaste elektrolytische proces.
Het wordt aanbevolen om voor kritische onderdelen experimenteel vast te stellen wat de juiste temperatuur en tijdsduur voor het verhittingsproces zijn. De maximale temperatuur dient altijd onder de ontlaattemperatuur van het behandelde product te blijven. Zodra de minimum temperatuur is bereikt, start de behandelingstijd.
Ondanks alle genomen maatregelen, die het risico voor waterstofbrosheid verminderen, kan dit risico bij de huidige elektrolytische processen nooit volledig worden uitgesloten. Als er geen enkel restrisico voor waterstofbrosheid mag bestaan, moet een andere methode voor corrosiebescherming worden gekozen (bijv. zinklamellen coatings).
Codeersysteem voor elektrolytisch aangebrachte oppervlaktebedekkingen
ISO 4042:1999 biedt een systeem met twee letters en een cijfer om het coatingtype voor bevestigingsmaterialen aan te geven. Voor de volgende editie van ISO 4042 is een nieuw systeem in ontwikkeling.
De huidige codes zijn als volgt opgebouwd:
- Eén hoofdletter voor het metaal van de coating, zie tabel 1
- Eén cijfer voor de minimale laagdikte (structuur van de laag), zie tabel 2
- Eén hoofdletter voor de glansgraad en de vervolgbehandeling, zie tabel 3
Table 1 is based on ISO 4042:1999

Tabel 2 is gebaseerd op ISO 4042:1999

Table 3 is gebaseerd op ISO 4042:1999
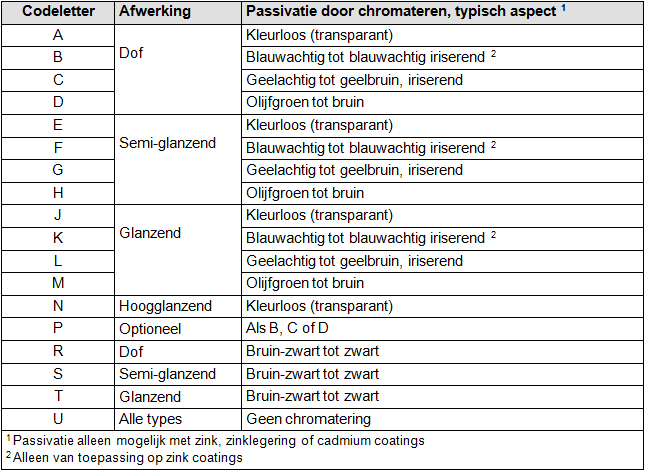
Voorbeeld van codering: A3L
“A” betekent verzinkt (zie tabel 1)
“3” geeft een laagdikte van minimaal 8 micron aan (zie tabel 2)
“L” wijst op een glanzende gele kleur (zie tabel 3)
Voorbeeld van gebruik in een productaanduiding: zeskantbout ISO 4014 – M16 x 60 – 8.8 – A3L.
Indien er geen specifieke eisen aan de laagdikte worden gesteld, zal de commercieel beschikbare laagdikte worden geleverd.
Beperkingen van de laagdikte
De mate van corrosiebescherming is over het algemeen proportioneel met de dikte van de toegepaste laag. Bij elektrolytische lagen op bevestigingsmaterialen is deze laagdikte echter niet altijd gelijk verdeeld (de distributie hangt onder meer af van de verhouding van de lengte en de diameter l/d). Voor de bescherming van een product is de minimale laagdikte normatief. Om te voorkomen dat de schroefdraad vastloopt tijdens montage, mag de laagdikte niet groter zijn dan 1/4 van de tolerantie (zie illustratie).

In de rechthoekige driehoek ABC is AB de laagdikte. De vergroting van de flankdiameter ten gevolge van de coating is:

Tabel 4 toont de maximaal toegestane laagdikte voor bevestigingsmaterialen met externe schroefdraad en tolerantiepositie g (vóór coating), in relatie tot de spoed van de schroefdraad en de nominale lengte.
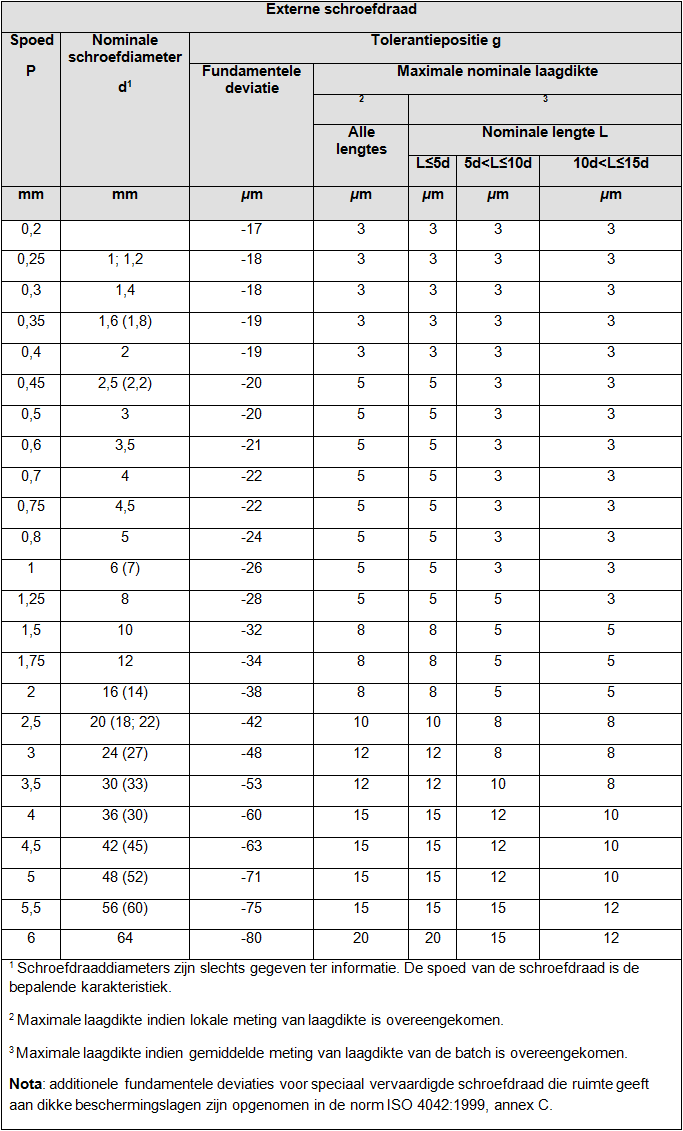
Meetpunten voor laagdikte
De minimale lokale laagdikte van bevestigingsmaterialen wordt gemeten op de punten in onderstaande afbeelding.
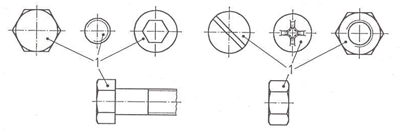
De gemiddelde laagdikte van een batch moet worden bepaald met de methode beschreven in ISO 4042:1999, annex D. Indien niet anders overeengekomen, moet de lokale laagdikte worden gemeten.