FEUERVERZINKUNG
Die Feuerverzinkung (Hot Dip Galvanizing (HDG)) ist ebenfalls eine gängige Oberflächenbeschichtung für Verbindungselemente aus Stahl. Sie liefert einen sehr soliden und nachhaltigen Korrosionsschutz. Die Feuerverzinkung für Stahlteile wird in der Norm ISO 1461 normiert, aber für Verbindungselemente gilt die Norm ISO 10684. Zusammengefasst ist der Prozess der Feuerverzinkung relativ einfach. Die Verbindungselemente werden in ein Bad aus geschmolzenem Zink getaucht (Normaltemperatur 455-480 °C, Höchsttemperatur 530-560 °C), gedreht, um das überschüssige Zink zu entfernen, und in Wasser abgekühlt, um das Zink zu festigen. Dies führt zu einer relativ dicken Zinkschicht (40 bis 70 Mikrometer) auf der Oberfläche der Produkte, im Vergleich zur galvanischen Verzinkung (3 bis 20 Mikrometer). Muttern werden auf die gleiche Weise behandelt, jedoch ist das Muttergewinde noch nicht geformt. Muttergewinde müssen immer nach der HDG gezogen werden. Dadurch bleibt das Innengewinde ungeschützt (ohne Zinküberzug), was aber keine nachteiligen Auswirkungen auf den Korrosionswiderstand hat, wie weiter unten illustriert wird. Der HDG-Prozess wird in der Regel für Verbindungselemente mit Durchmessern von 8 oder größer als geeignet betrachtet.
Die hohe Zinkmenge liefert einen exzellenten Korrosionswiderstand unter normalen Außenbedingungen, aber der Nachteil ist, dass die Schichtdicke den zulässigen Gewindespielraum erheblich übersteigt und dies ein Problem für alle Schraub-Verbindungselemente darstellt.
Um dieses Problem handzuhaben, liefert die Norm ISO 10684 zwei Lösungen. Beide beinhalten die Änderung der Abmessungen der Schraubverbindungen.
Eine Lösung ist ein System, bei dem das Verbindungselement mit Außengewinde (Schraube) mit einer größeren grundsätzlichen Abweichung gefertigt wird (das Gewinde ist geringfügig dünner). Nach der Galvanisierung wird die Schraube mit einem Innengewinde mit einer Gewindetoleranz der Klasse 6H (der „normalen“ Toleranz) versehen. Die Grenzwerte für die Außengewinde dieses Systems werden in der ISO-Norm 965-4 mit einer Gewindetoleranz der Klasse 6az (vor der Galvanisierung) festgelegt und das System wird als ISO fit HDG-System bezeichnet. Schrauben werden mit der Festigkeitsklasse und einem zusätzlichen „U“ gekennzeichnet.
Die andere Lösung, festgelegt durch ISO-Norm 10684, ist es, das Innengewinde (Mutter) ein wenig größer zu ziehen (Übergröße), sodass es zum galvanisierten Verbindungselement mit Außengewinde (Schraube) passt – das so genannte Oversize HDG-System. Die Grenzwerte der Mutter-Übergröße werden in der ISO-Norm 965-5 festgelegt, die Gewindetoleranzklasse der größer gezogenen Muttern ist 6AZ. Muttern werden mit der Festigkeitsklasse und einem zusätzlichen „Z“ gekennzeichnet.
Beachten Sie bitte, dass die zwei Systeme nie kombiniert werden dürfen, da dies zu Passformproblemen (übergroße Schraube mit ISO-konformer Mutter) oder einer kritischen Festigkeitsreduzierung der Schraubverbindung (ISO-konforme Schraube mit übergroßer Mutter) führen kann.
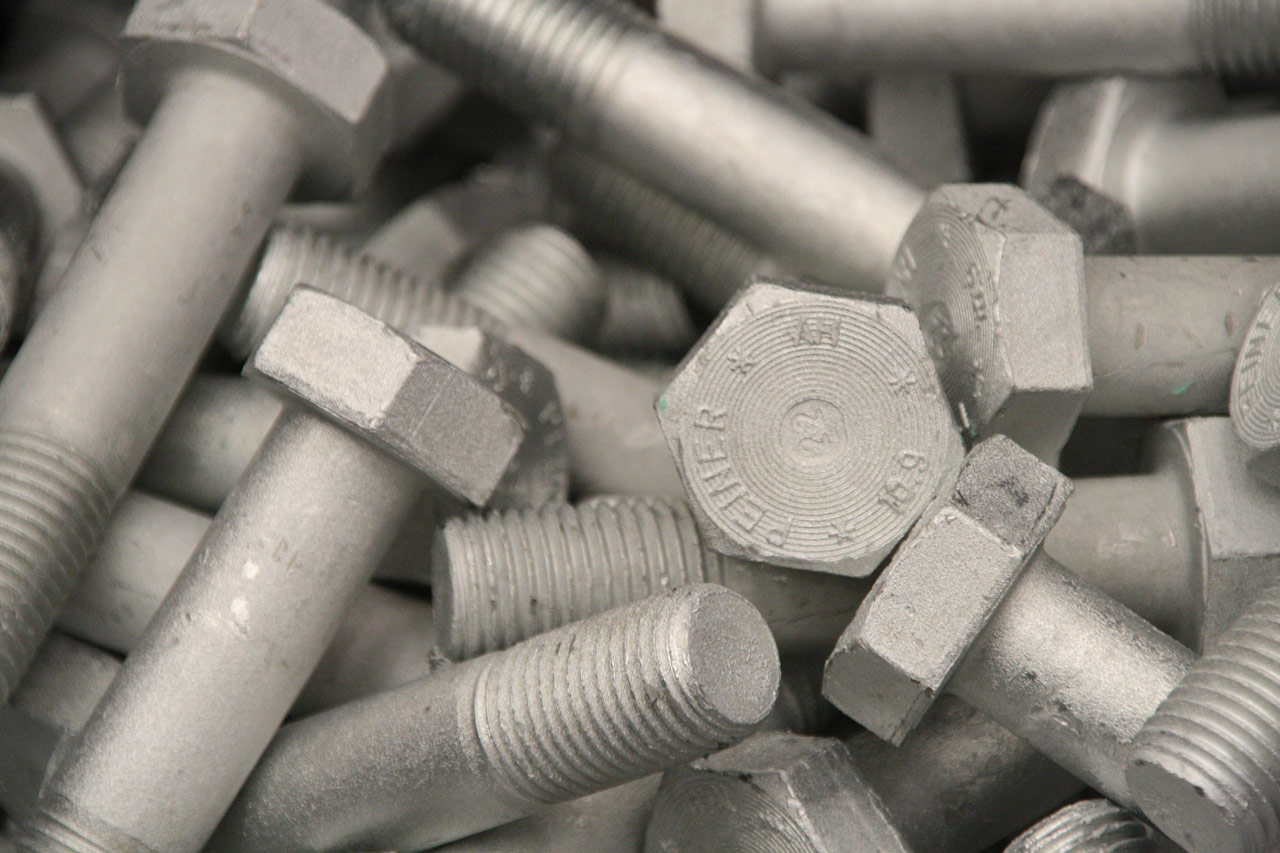
Quelle: Thielco Metallbeschichtung
Belastbarkeit der Schraubverbindungen
Grundsätzlich kann gesagt werden, dass die mechanischen Eigenschaften der Schrauben der ISO 898-1 entsprechen und die Muttern konform ISO 898-2 durch die Feuerverzinkung nicht beeinträchtigt werden. ISO 10684 macht nur eine Ausnahme für die Durchmesser M 8 und M 10 (in Anhang A). Für diese Abmessungen ist die Belastbarkeit um ca. 20 % reduziert. Siehe EN 10684 für die Details.
Allerdings wird für die in der Regel immer noch verwendeten Muttern konform DIN 934, HDG konform der (veralteten) DIN 267-10 angewandt und diese Norm erlaubt eine Reduzierung der Belastbarkeit aller HDG-Verbindungselemente. Die Belastbarkeit einer Mutter-Schrauben-Kombination mit Muttern konform DIN 934 wird mit ca. 5 % für die größte Größe M36 reduziert und dieser Wert erhöht sich stufenweise bis zu 20 % für die kleinste Größe M6. Für weitere spezifische Werte verweisen wir auf DIN 267-10. Aufgrund der Abweichung der Gewindetoleranzen darf das Schraubgewinde der Schraube bei Mindest-Zugbelastung beschädigt werden.
Atmosphärische Korrosion auf feuerverzinktem Stahl
Wenn der Überzug der Atmosphäre ausgesetzt ist, bildet sich eine Korrosionsschicht (Zinkpatina), die überwiegend aus Zinkkarbonat besteht, was weitere Korrosion verzögert, da es nahezu unlöslich ist. Wenn galvanisierter Stahl für längere Zeit feucht bleibt und nicht genug Luftzirkulation vorhanden ist, entwickelt sich ein weißes, voluminöses Zinkkorrosionsprodukt, „weißer Rost“, der aus ästhetischen oder Lackiergründen weniger wünschenswert ist. Die Bildung von weißem Rost kann durch angemessene Lagerung und Verpackung oder, wenn notwendig, durch Ölen des Zinks oder Passivieren in Chromsäure unterdrückt werden.
Einfluss des Klimas auf den Zeitraum, in dem feuerverzinkter Stahl geschützt bleibt
Der Zeitraum, für den Stahl vor Korrosion geschützt ist, verhält sich proportional zur Dicke der Zinnschicht und ist von den Klimabedingungen abhängig; siehe nachfolgende Grafik. Grundsätzlich wird der Zeitraum, in dem eine Zinkschicht Schutz bietet, interpretiert als Zeitpunkt, ab der Belastung bis zu dem Zeitpunkt, an dem auf dem Basismetall Korrosion („roter Rost“) an mehr als 5 % der Oberfläche zu sehen ist.
Korrosionswiderstand bei klimatischen Einflüssen:
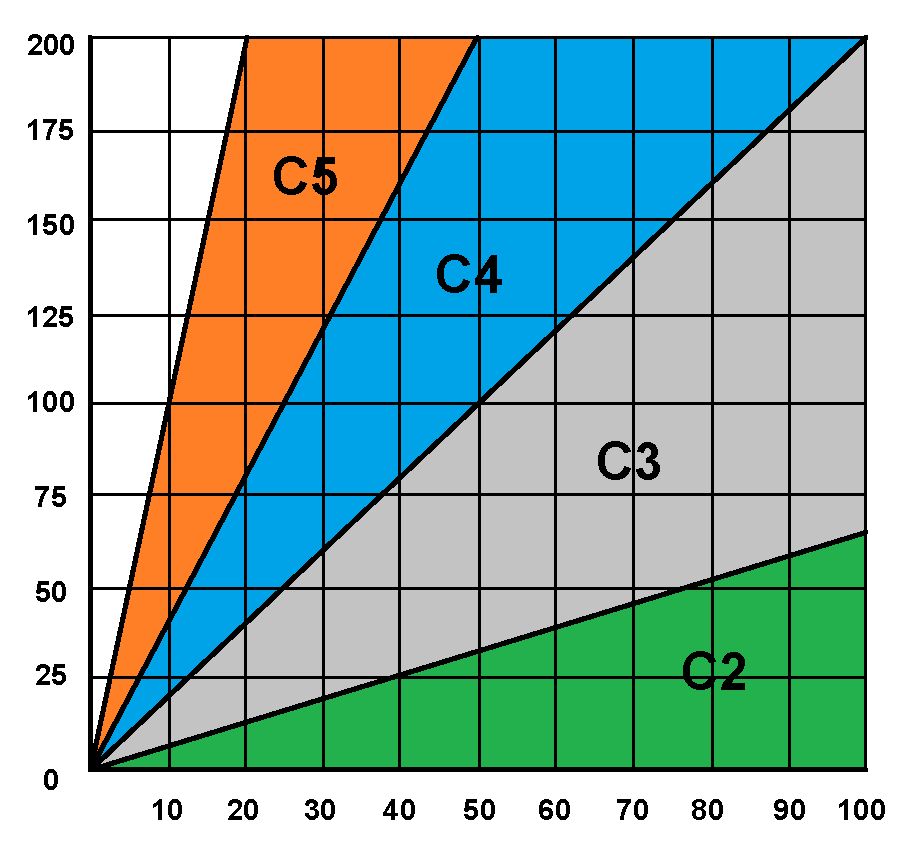
C2 - Kontinentalklima
C3 - Großstadtumgebungen
C4 - Mäßiges Industrie- oder Küstenklima
C5 - Aggressives Industrieklima
Diese Grafik präsentiert aufgrund unvorhersehbarer örtlicher Einflüsse nur grobe Annäherungswerte.
„Selbstheilende“ Effekte feuerverzinkter Verbindungselemente
Wenn die Zinkbeschichtung zerkratzt oder abgeblättert ist, versucht die Zinkschicht den beschädigten Bereich unter normalen atmosphärischen Bedingungen zu bedecken.
Weil Zink weniger edel als Eisen (Stahl) ist, löst sich zunächst das Zink und schützt den Stahl vor Korrosion, bis das ganze Zink aufgelöst wurde.
An Stellen, an denen in der Zinkschicht Öffnungen von 1,5 bis 2 mm Größe vorhanden sind oder an kahlen Flächen bis zu 10 mm2, bleibt der Stahl aufgrund eines elektrochemischen Prozesses, genannt „kathodische Überbrückung“, geschützt. Das Zink liefert einen wesentlichen Schutz und die ungeschützten Bereiche werden mit einer Struktur aus Zinksalzen abgedeckt. Ein gutes Beispiel für dieses Phänomen sind Schraubgewinde feuerverzinkter Muttern, die nach der Galvanisierung gezogen worden sind. Die Zinkschicht am Schraubgewinde übernimmt den Schutz des unbeschichteten Muttergewindes. Ein weiterer wichtiger Aspekt des kathodischen Schutzes ist, dass keine Korrosion unterhalb der Zinkschicht auftritt.
Eine schematische Darstellung der „Kathodischen Überbrückung“:

Lackierung feuerverzinkter Oberflächen
Ein so genanntes Duplex-System ist eine Kombination aus Feuerverzinkung und Lackierung. Es bietet eine gute Lösung in sehr aggressiven Atmosphären (z. B. am Meer oder in einer sauren Umgebung), wenn Wartung und Reparaturen praktisch unmöglich ausführbar sind, oder wenn eine spezielle Farbe gewünscht wird. Dieses System kann einen 1,5 - 2,5 x längeren Schutz als die Summe beider einzelnen Systeme bieten. Bei fachgerechter Entfettung bietet die Feuerverzinkung eine gute Haftung für viele Lacktypen.