Electro cincado - o Cincado
Este es tratamiento de superficie más común para artículos de fijación de acero. Una capa muy fina (3 a 20 micras) para los roscados de zinc o una aleación de cinc (por ejemplo, ZnFe, ZnNi) se deposita en la superficie del artículo de fijación por un proceso electrolítico (galvánico). Directamente después de que los productos se cubren con zinc, una capa de pasivación se realiza en el cinc - o en la aleación de cinc, que sirve como protección para el cinc o la aleación de cinc. Hay muchos tipos diferentes de pasivación, con diferentes colores y protección, ofreciendo varios elementos de fijación electro cincados o con aleación de cinc..
*un micrón o μm es 0,001 milímetros.
El proceso electro cincado
Como muestra la imagen anterior, los artículos de fijación se colocan en un tambor giratorio plástico, sumergido en un tanque lleno con un electrólito (fluido conductor) y cargado negativamente (cátodo). Barras o hojas de Zinc- o aleación de zinc están presentes en el tanque y se cargan positivamente (ánodo), y la corriente eléctrica transportará los iones de cinc o aleación de cinc para os artículos de fijación cargados negativamente.
El cinc o las aleaciones de cinc son menos nobles que el acero. Si se utiliza como revestimiento protector en aceros, actúan como ánodo que proporciona electrones al acero, si ocurre en un ambiente húmedo. Esto se llama protección catódica.
Cobre, latón, níquel, cromo, estaño y plata son más nobles que el acero. Si estos metales nobles se utilizan como revestimiento protector, actúan como cátodo. Como consecuencia, el acero puede ser atacado directamente e puede ocurrir corrosión incluso bajo el revestimiento si la humedad entra en contacto con el acero (ánodo) a través de poros, o daños en el revestimiento.
Es por eso que el cinc o aleaciones de cinco son los metales de revestimiento más utilizados para productos de acero.
Pasivación
La protección contra la corrosión ofrecida por el revestimiento de cinc o aleaciones de cinc puede mejorarse considerablemente, haciendo la pasivación en los productos. En la forma clásica de este tratamiento, es una capa cromada extremadamente fina (aproximadamente 0,1 µm) que sella los poros del revestimiento de cinc o aleación de cinc y conecta el oxigeno al revestimiento. Esta capa contiene a menudo cromo hexavalente (Cr(VI)) y por lo tanto, posee una propiedad única de “autor regeneración”. En caso de daño mecánico, sales de cromo hexavalentes solubles dentro de la capa de pasivación repararán (re-passsivar) las áreas expuestas. La desventaja de este tratamiento es que Cr(VI) es considerado un tratamiento peligroso, substancia no amiga del ambiente (tóxico y cancerígeno). Su uso en la UE es limitado y el Cr (VI) ha sido gradualmente prohibido por varias legislaciones (por ejemplo. RoHS, ELV (ver links al final de este documento)). Los detalles sobre el revestimiento se pueden encontrar en la norma lSO 4520.
Dependiendo del grosor y la composición de la pasivación, la color varía de transparente (blanco), azul, amarillo, hasta negro.
Pasivación blanco/azul
Este es el tipo más común, ofreciendo baja protección contra la corrosión, y por lo tanto, recomendado para aplicaciones internas.
Pasivación en negro
El mismo nivel de protección que la pasivación blanca/azul y principalmente escogida por su color negro. Contiene Cr(VI).
Pasivación en amarillo
Este tipo de pasivación ofrece una mejor resistencia a la corrosión y generalmente es aconsejable para aplicaciones exteriores, sin embargo disminuye en popularidad, pues el contenido de Cr(VI) es significativo.
Pasivación en verde
Estos tipos de pasivación son principalmente para aplicaciones militares. La resistencia a la corrosión es comparable o ligeramente mejor do que la pasivación amarilla, y también contiene Cr(VI).
Pasivación con cromo trivalente (Cr(III))
Como resultado de la legislación sobre sustancias peligrosas, como RoHS, Reach y ELV, se ha desarrollado un nuevo tipo de pasivación. Esta nueva pasivación no puede contener Cr(VI). En vez de Cr(VI), presente en la pasivación negra, amarilla y verde, la mayoría de las pasivaciones recién-desarrolladas usan cromo trivalente (Cr(III)). Algunas de estas pasivaciones todavía poseen mejor resistencia a la corrosión que la pasivación con Cr(VI). A menudo se refiere como ‘pasivación espesa’, Una capa fina puede tener un grosor de 0,08 a 0,1 µm, y una capa gruesa puede medir 0,2 a 0,3 µm. La pasivación transparente fina se utiliza corrientemente. Las pasivaciones espesas son iridiscentes (azulado-amarillento-verdoso en cinc, amarillento-verdoso en aleación de cinco) y ofrecen resistencia a la corrosión superior, mejor que la pasivación amarilla con Cr(VI). Para mejorar aun más la resistencia a la corrosión y/o mejorar el aspecto del revestimiento, un sellador puede aplicarse.
Disfunción hidrogénica
El proceso de electro-cincado utiliza electricidad para precipitar el cinc o aleaciones de cinc. La corriente causa también la electrólisis del agua en el baño, separando el hidrogeno y el oxigeno.
El oxigeno desaparece del líquido en el baño, pero los iones de hidrogeno pueden difundirse en el metal de los artículos de fijación y unirse a las moléculas de hidrogeno. Esto es acompañado por un aumento de volumen, que causa un aumento de estrés en la estructura metálica. En presencia de fuerzas de tensión externas, esto puede dar lugar a fracturas tardías, espontáneas y quebradizas. Po otro lado, el decapado sin inhibidores (decapado como el utilizad en el proceso de galvanización en caliente) y el proceso no calificado de tempera de aceros, con altas propiedades mecánicas, también puede inducir la disfunción hidrogena.
= iones de hidrógeno
El peligro de la disfunción hidrogénica se aplica a los productos:
- con fuerza de tracción ≥ 1000 MPa
- con dureza ≥ HV320
- con endurecimiento
Para reducir el riesgo de disfunción hidrogénica al mínimo, estos productos deben ser recalentados (recocido) después del proceso de electro cincado por cierto período de tiempo y a una cierta temperatura. La norma internacional para revestimientos electro cincados en artículos de fijación, ISO 4042 edición 1999, declara (entre otras cosas) que piezas electro cincadas deben ser recocidas dentro de las 4 horas, pero de preferencia dentro de una hora después de la electro cincagem y antes de la pasivación, a una temperatura parcial de 200°C a 230°C. La temperatura máxima debe tener en cuenta el material de revestimiento y el tipo de material base.
Con el aumento del grosor del revestimiento, la dificultad de remover el hidrógeno aumenta. la introducción de un proceso de recocido intermediario cuando el revestimiento es sólo de 2 µm a 5 µm puede reducir el riesgo de disfunción hidrogénica.
La norma ISO 4042 no proporciona las condiciones de recocido exactas. Ocho horas se consideran un ejemplo típico de duración de recocido. Sin embargo, las duraciones de cocción en el rango de 2h a 24h a 200°C a 230°C pueden ser adecuadas según el tipo y tamaño de las piezas, geometría, propiedades mecánicas, procesos de limpieza y procesos electro cincados usados.
Para componentes críticos, se recomienda que la temperatura y el tiempo se establezcan experimentalmente, sin embargo, la temperatura del recalentamiento nunca debe exceder la temperatura de la tempera. El tiempo de recalentamiento comienza tan pronto como los productos alancen la temperatura mínima.
A pesar de todos los cuidados, los actuales procesos de electro cincado pueden reducir el peligro de la disfunción hidrogénica, pero no se puede eliminar completamente. Si para aplicaciones críticas, y las que no puede existir ningún riesgo, se debe elegir otro método de recubrimiento (por ejemplo, revestimientos zinc flake).
Sistema de codificación para electro cincado
De acuerdo con la norma ISO 4042:1999 los revestimientos electro cincados se denominan por un código compuesto por dos letras mayúsculas y un número. Se está preparando un nuevo sistema de codificación para la próxima edición de la ISO 4042.
El código actual se construye de la siguiente manera:
- Una letra mayúscula para el revestimiento de metal, ver tabla 1
- Un número para el espesor mínimo de revestimiento (estructura de revestimiento), ver tabla 2
- Una letra mayúscula para el grado de brillo y tratamiento, ver tabla 3
Todas las tablas basadas a la ISO 4042:1999
TABLA 1
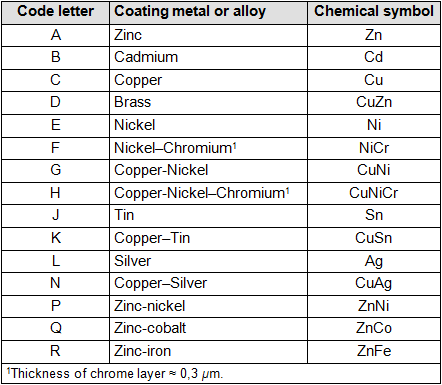
TABLA 2

TABLA 3

Ejemplo de codificación: A3L
“A” significa cincado (ver tabla 1)
“3” indica el espesor de revestimiento de al menos 8 micras (ver tabla 2)
“L” refiere una pasivación de amarillo brillante (ver tabla 3)
Ejemplo de designación: tornillo hexagonal DIN 931 – M16 x 60 – 8.8 – A3L.
Si no se ajusta ningún espesor de revestimiento, se proporciona el grosor de revestimiento disponible comercialmente.
Restricciones de espesor de revestimiento
El grosor de protección contra la corrosión es generalmente proporcional al grosor del revestimiento aplicado. Sin embargo, con revestimientos electro cincados en artículos de fijación, el espesor no se distribuye igualmente (es, entre otras cosas, dependiente de la relación entre longitud y diámetro l/d). Para la protección de un artículo, el grosor mínimo de la capa de revestimiento es normativo. Para evitar que gripen tuerca/tornillo durante el montaje, el espesor del recubrimiento máximo nominal no debe exceder 1/4 de la tolerancia (figura seguirte).


Comprobación de la capa de revestimiento
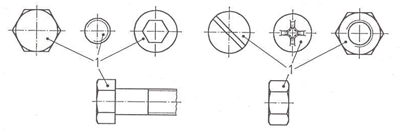
El espesor medio de la capa de revestimiento de un lote debe determinarse utilizando el método descrito en la norma ISO 4042, anexo D. Salvo acuerdo en contrario, se debe medir el grosor de la capa de revestimiento.